Dry powder filling machines are essential equipment in industries that require precise filling of powdered products, particularly in pharmaceuticals. These machines ensure that powdered substances are dispensed into containers accurately and efficiently. Understanding how they work provides insights into their role in improving productivity and ensuring product safety. In this article, we’ll explore the step-by-step process of how these machines operate and discuss some key technologies and innovations in the field.
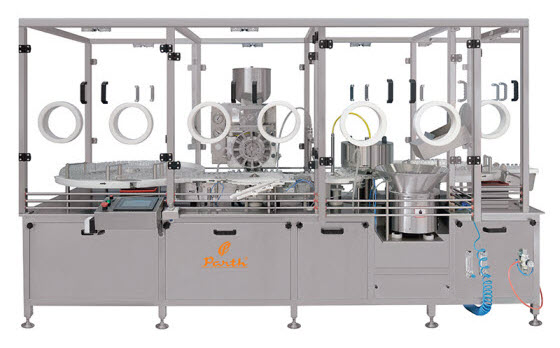
Introduction to Dry Powder Filling Machines
A dry powder filling machine is a specialized device used to fill containers such as vials, bottles, or capsules with precise quantities of powdered substances. These machines are particularly common in pharmaceutical production, where the accurate dosing of medications is critical. Modern machines have evolved to offer automated and semi-automated solutions that reduce human error and increase production speed.
The operation of these machines involves several stages, from feeding the powder into the machine to sealing the containers. Let’s walk through the step-by-step process.
Step 1: Powder Feeding and Dispensing
The first step in the dry powder filling process is feeding the powder into the machine. This is typically done using a hopper, which holds a bulk amount of the powdered product. The hopper continuously feeds powder into the dosing unit, ensuring there’s a constant supply available for filling.
At this stage, the machine measures the required amount of powder for each container. This step is highly automated in most systems, especially in advanced machines like the dry powder filling stoppering machine. Precision is key, as even slight variations in the amount of powder can compromise the product’s efficacy or result in waste.
Step 2: Powder Dosing
Once the powder has been fed into the system, the machine doses it into predetermined quantities. This is often accomplished using volumetric or gravimetric filling techniques. In volumetric filling, the machine uses specific volume measurements to dispense the powder, while gravimetric filling involves measuring the powder by weight.
Machines like the dry powder filling and stoppering machine excel at ensuring that the exact quantity of powder is dispensed into each vial or container. The level of precision is critical, especially in pharmaceutical applications where correct dosage affects the product’s safety and effectiveness.
Step 3: Container Handling and Positioning
The containers, which are typically vials or bottles, are introduced into the system through a conveyor belt or rotary table. In an automated setup, the machine ensures that the containers are correctly positioned beneath the filling nozzle.
Dry powder filling lines often include mechanisms to align and stabilize the containers, preventing spillage or misalignment during the filling process. This positioning is crucial to ensure that every vial is filled evenly and accurately.
Step 4: Powder Filling
With the containers in place, the actual filling begins. The filling nozzle dispenses the pre-measured dose of powder into each container. Depending on the design of the machine, this step can occur in multiple filling heads simultaneously, significantly increasing production speed.
For example, the dry powder filling and sealing machine is designed to handle high-speed operations, allowing for multiple containers to be filled in parallel. The accuracy of these machines ensures that each container receives the exact same amount of powder, which is critical for consistency in pharmaceutical products.
Step 5: Stoppering or Sealing
Once the containers are filled with the powdered substance, they need to be sealed. Sealing ensures that the powder remains sterile and uncontaminated. In many systems, this is done using a stoppering machine, which applies stoppers or caps to the containers immediately after filling.
Dry powder filling and stoppering lines are equipped with advanced stoppering mechanisms that ensure the vials are sealed tightly, preventing air or moisture from entering. These machines are crucial in maintaining product integrity, particularly for medications that need to be kept in a sterile environment.
Step 6: Sealing and Final Closure
For products that require additional sealing after stoppering, machines like the dry powder filling and sealing machine come into play. These systems apply a final seal, often using a metal crimp or heat seal, to further protect the product.
Sealing technology has advanced to ensure tamper-proof packaging and reduce contamination risks. In industries such as pharmaceuticals, where safety and hygiene are top priorities, these sealing methods are non-negotiable.
Step 7: Inspection and Quality Control
Once the containers are filled and sealed, many machines are equipped with quality control mechanisms that inspect the final product. This inspection checks for proper fill levels, correct sealing, and any defects in the containers.
Modern machines often incorporate sensors and cameras to ensure that each vial meets stringent quality standards. Any container that does not meet the criteria is automatically rejected, ensuring that only the highest quality products move on to the next stage of production.
Step 8: Labeling and Packaging
After passing the inspection phase, the containers are typically labeled and prepared for packaging. The labeling process is essential for traceability, ensuring that each product can be identified and tracked throughout its lifecycle.
In some setups, the machine integrates with a broader dry powder filling line that includes packaging systems. These systems handle everything from placing the vials in trays or cartons to shrink-wrapping and preparing them for shipment.
Technologies in Modern Dry Powder Filling Machines
The technology behind dry powder filling machines has evolved significantly, particularly in the areas of automation, accuracy, and speed. Servo-based technologies are now common, allowing for precise control over the filling and stoppering processes. Machines like the Dry Powder Injection Filling Machine are built with advanced servo systems that offer high precision and consistency.
Another important innovation is the integration of Dry Powder Filling Bunging Machines, which further streamline the process by combining filling, stoppering, and bunging in a single machine. These machines improve efficiency, reduce manual intervention, and minimize contamination risks.
Applications of Dry Powder Filling Machines
While dry powder filling machines are most commonly associated with the pharmaceutical industry, they also find applications in other sectors such as food, cosmetics, and chemicals. In any industry where precision dosing of powders is required, these machines play a critical role.
In pharmaceuticals, the ability to handle sterile powders and ensure consistent dosing is vital for injectable medications. For example, the Dry Powder Injection Filling Line is specifically designed to handle sterile powders for injectable drugs, ensuring that each vial meets the necessary safety standards.
Conclusion
Dry powder filling machines play an indispensable role in industries where precise powder handling is critical. From feeding and dosing to sealing and inspection, these machines have evolved to offer unparalleled accuracy and efficiency. Technologies such as servo motors, automation, and integrated stoppering mechanisms continue to advance, making these machines faster and more reliable.
Whether it's a dry powder filling stoppering machine or a more advanced dry powder filling and sealing machine, these technologies are essential for maintaining the quality and safety of powdered products in industries such as pharmaceuticals. By understanding the step-by-step process of how these machines work, manufacturers can better appreciate the impact these advancements have on production efficiency and product safety.
FAQs - Dry Powder Filling Machine
A dry powder filling machine is used to precisely fill containers like vials or bottles with powdered substances, commonly in industries like pharmaceuticals.
It dispenses pre-measured powder into vials and then seals them using a stopper, maintaining the sterility of the product.
These machines are widely used in pharmaceuticals, but they are also found in food, cosmetics, and chemical manufacturing.
Servo-based machines offer high precision, flexibility, and consistency, improving the overall efficiency of the filling process.
Automation reduces human error, increases production speed, and ensures consistent filling and sealing, making the process more efficient and reliable.