In the fast-paced world of pharmaceutical manufacturing, the expectations for precision, sterility and efficiency continue to grow. For facilities producing lyophilized or dry injectable formulations, the injectable powder filling process is a critical operation that demands accuracy, consistency and minimal human contact. Traditional manual or semi-automatic systems, although reliable for low-volume production, often fall short when it comes to scaling up and meeting contemporary regulatory and operational requirements.
This is where an automated injectable powder filling system proves its value. From reducing human error to increasing line throughput, modern solutions like the Automatic Servo Base Injectable Powder Filling Machine are purpose-built to deliver performance with precision - especially when dealing with powders.
Below are five key reasons pharmaceutical companies should consider upgrading to a Servo Base Injectable Powder Filling Machine.
Enhanced Accuracy and Fill Consistency of Injectable Powder Filling System
One of the most significant advantages of automated systems is the superior accuracy they offer in dosing powder formulations. Unlike manual filling, which depends heavily on operator skill and judgment, automated systems utilize servo motors and precise mechanical assemblies to ensure exact dosing.
How Automation Improves Fill Accuracy:
- Servo-driven systems respond to real-time commands, ensuring repeatability down to microgram levels.
- Dynamic adjustments during filling prevent underfill and overfill scenarios.
- The system can maintain fill volume within a very narrow range, critical for injectable formulations.
This level of control is especially important for injectable powder filling and stoppering machines, where even minor deviations can impact dosage efficacy, vial vacuum conditions or reconstitution behavior.
Significant Reduction in Human Error and Contamination Risk
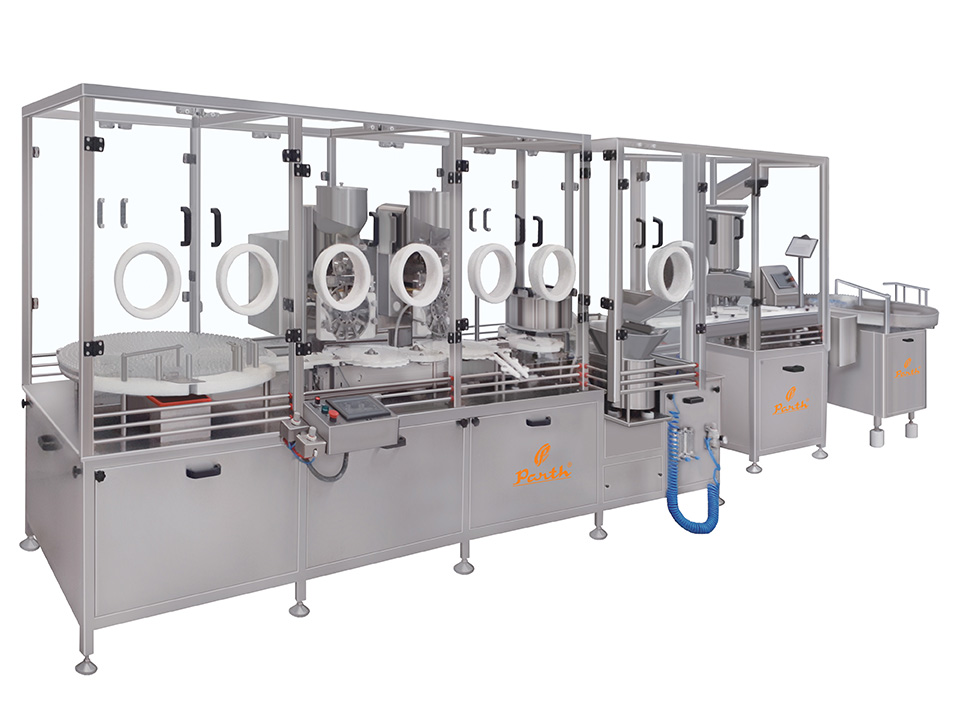
Manual filling inherently involves more human interaction, which increases the risk of contamination and procedural error. Automated systems are designed to minimize operator intervention and optimize aseptic processing.
Benefits of Reduced Human Involvement:
- Consistent and hands-free operation under controlled environmental conditions.
- Touchscreen HMIs allow for parameter setting and real-time monitoring without opening sterile enclosures.
- Sealed systems reduce exposure of product and components to external environments.
A servo base injectable powder filling machine ensures that once parameters are programmed, the process runs seamlessly, with minimal operator input and fewer error-related downtimes.
Faster Throughput for Injectable Powder Filling Machine Large Batch Production
In growing pharmaceutical facilities, speed is often a bottleneck - especially when working with limited filling capacity. Upgrading to an automated injectable powder filling line can increase production rates significantly without compromising on accuracy or quality.
Speed-Enhancing Features of Automated Systems:
- Multi-head filling & Multi Dosing Configuration capable of processing several vials simultaneously.
- Continuous vial handling via rotary or linear transport mechanisms.
- Integrated stoppering stations that operate in tandem with filling units to maintain line speed.
Advanced designs often include dual-tracked auger drives, increasing operational efficiency by doubling output while maintaining controlled dosing. This is particularly useful for vaccine production, lyophilized antibiotics and biosimilars where batch sizes are large and turnaround time is short.
Seamless Integration with Stoppering and Sealing Units
A standalone filler can only do so much. Upgrading to a complete injectable powder filling and stoppering machine ensures that vials are processed from filling to closure in a synchronized and sterile environment.
Integrated System Advantages:
- Automatic stopper pick-and-place mechanisms eliminate manual transfer.
- Vacuum-assisted insertion ensures stoppers are seated correctly every time.
- Coordinated vial indexing systems align stoppering with fill timing for maximum efficiency.
Integrated servo base systems offer real-time feedback for each step, allowing operators to track the process in a unified control interface. By eliminating the need for multiple machines and manual handling between operations, these systems streamline production of the manufacturing line.
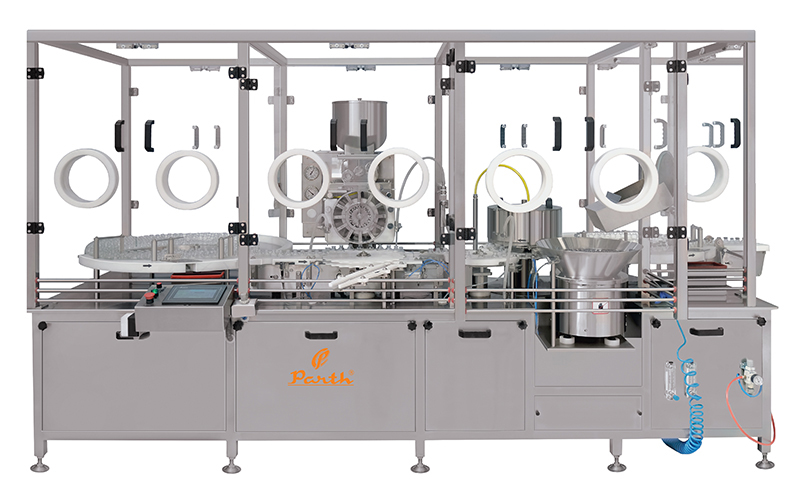
Greater Flexibility, Easy Maintenance and Data Control
Modern automated injectable powder filling machines are designed not only for performance but also for adaptability and user-friendliness. They allow fast changeovers, are easier to clean and are equipped with digital monitoring systems.
Operational and Maintenance Advantages Include:
- Quick-change format parts for different vial sizes and fill weights.
- Clean-in-place (CIP) and sterilize-in-place (SIP) functionality in higher-end models.
- Modular design allows for scaling up or retrofitting new features without full replacement.
- Data logging and real-time process visualization via HMI ensure better process transparency and documentation.
For facilities operating multiple products or variable batch sizes, this flexibility can significantly reduce setup and maintenance time - saving both labor and cost in the long run.
Additional Considerations When Upgrading
When investing in an automated filling system, look for:
- Compatibility with current line configurations.
- Ease of validation and calibration.
- Availability of service and spare parts.
- Technical support and training options for operators and maintenance staff.
Choosing a high-quality injectable powder filling machine from a trusted manufacturer can extend equipment life and reduce the total cost of ownership.
Conclusion
Upgrading to an automated injectable powder filling system is no longer a luxury for high-volume producers - itâs a strategic necessity. As the industry pushes toward greater output with fewer resources, automation delivers the accuracy, reliability and efficiency required to stay competitive.
From consistent dosing and high-speed operation to integrated stoppering and real-time monitoring, machines like the Automatic Servo Base Injectable Powder Filling Machine are redefining how injectable products are manufactured. Whether you're modernizing your current setup or launching a new product line, investing in automation provides long-term operational gains and ensures consistent, scalable quality.
FAQs About Dry Syrup Filling Machine
Upgrading to automation improves accuracy, reduces human error, increases throughput and ensures consistency in injectable formulations.
Automated systems, like servo-driven auger mechanisms, provide precise dosing and dynamic adjustments to prevent underfill or overfill, ensuring accurate results.
Automation minimizes human intervention, reducing contamination risks and ensuring consistent, hands-free operation under controlled conditions.
Yes, automated systems can process larger batches faster through multi-head configurations and synchronized filling and stoppering operations, enhancing production speed.
Automated systems offer quick-change parts, easy cleaning functions and real-time monitoring for better process control, leading to reduced downtime and maintenance costs.