If you have a cartoning machine at your facility, you need to understand how it works and what to do when you notice any problems. Cartoning machines are used in a wide variety of industries for packaging purposes. They are designed to boost productivity and sidestep the tiresome work involved in manually forming and loading cartons.
Selecting the Ideal Cartoning Machine
Cartoning machines, commonly referred to as cartoners, are used to erect, fold, side-seam, and close and seal cartons. They can be semi-automatic or fully automatic.
When choosing a cartoning machine, it’s important to consider the type of product you plan to pack and your budget. This will help you choose the right machine for your business.
Optimizing Conveyor Performance
Getting your conveyor’s feed rate right is crucial for maximizing your throughput. The speed of the belt should match the rotational speed of your spindle.
To find your conveyor’s feed rate, divide the linear speed in m/s by the circumference of your drive drum in metres to get RPM. Multiply that number by the angular rate in radians per second to calculate the conveyor’s throughput in litres/min.
During the cartoning process, you need to keep in mind that you need to set the feed rate correctly. This will help you to reduce the risk of errors. You can do this by adjusting the conveyor chain plate to match the width of the carton. You can also modify the storeroom as well.
Enhancing Productivity with Cartoning Machines
Cartoning machines are an effective solution for boosting productivity in your production process. These equipment complete packaging operations faster and with higher precision than human employees. In addition to helping your company save money, cartoning equipment can also help you avoid costly mistakes that occur when human workers are involved in the process.
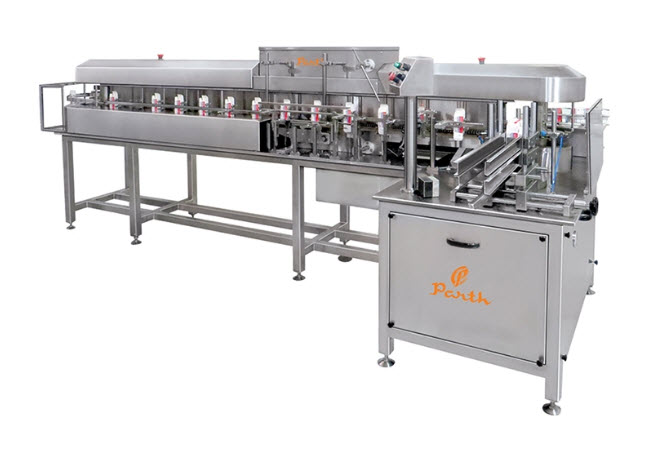
Versatile Cartoning Machines
Cartoning machines are used in different industries such as food, chemical and cosmetics. They are known for their durability and ease of use.
The machine erects, folds, side-seam, closes and seals cartons. It inserts the product into a carton’s open end before sealing flaps by tucking or applying adhesive. A cartoning machine is equipment that makes special packaging boxes for different products. It uses light, electrical and pneumatic configurations to make the packages.
They can save time and reduce labour costs by automating the packaging process. They can also be used in conjunction with other machines to complete a production line. It’s important to match the type of machine you need with your production capacity.
Maintaining Cartoning Machine Performance
A cartoning machine is a piece of equipment that can erect, close, fold, and side seam a carton. It is commonly used in a wide range of applications, including pharmaceuticals, food, cosmetics, and sundry goods.
A good filter is an important part of any cartoning machine. It keeps circulating fluids free of particles and contamination, which prevents valves, pumps, and hydraulic components from failing or becoming damaged.
When checking the filters, look for signs of wear such as small cuts or slits in the pleats. You may also want to examine the center tube to see if it has collapsed or buckled. If so, this is the filter that you should replace in the future. Another sign that a filter is on its way out is if there is a noticeable loss of airflow, which could mean that there is a hole in the pleats or a bad seal around the center tube.
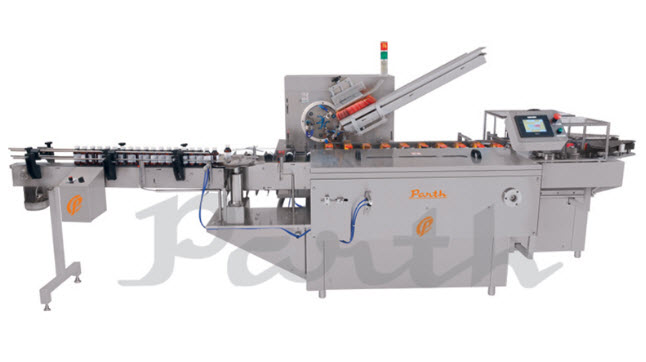
Ensuring Effective Cartoning Machine Performance – Checking the Hot Melt Adhesive
One of the most common and important issues to address when maintaining your cartoning machine is to check the hot melt adhesive. If the adhesive is burning or cracking, it can cause production halts and affect the quality of the glue bond.
The viscosity of the adhesive can also change. This can lead to a problem called phase separation. This is caused by the polymer base of the adhesive being affected by heat, temperature changes, etc.
The application temperature of the hot melt is very important. It must be above the minimum temperature that the substrate will see in service. This is especially important with textiles that are heat sensitive. It can lead to loss of adhesive strength and even a complete melt of the glue.